
Copied!

Cynthia Stuebner
How grant managers can increase trust and transparency

John Higgins
Less code is the key to greater innovation and business agility – Pega Blueprint leads the way
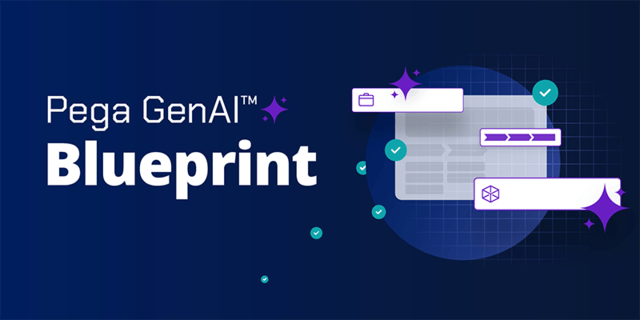
Kerim Akgonul
Blueprint your next workflow, today

Satya Narayan Mishra
Pega Global Operations Center powers Pega Cloud

Michelle Mitchell
How to overcome the challenges of adopting AI in your call center

Alina Popa
International Women’s Day 2024

Norma Suarez
Real time – real value: A guide to Real-Time Interaction Management (RTIM)

Rafeeq Lorick
Envisioning personal accountability

Tara DeZao
How to improve customer lifetime value with exceptional experiences

Tara DeZao
How adaptive analytics is transforming customer experience

John Higgins
Reflections from WEF Davos 2024: Navigating the GenAI Frontier

Tara DeZao
Responsible AI is a winner for everyone

Michelle Mitchell
The top 10 uses of AI for customer engagement

Kat Austin
AI in customer service: What your organization should know

Tara DeZao
Reduce waste with AI-powered identity optimization

Peter van der Putten
Why we all need an AI manifesto

Kyle Munderville
How hyper-personalization helps improve the customer experience
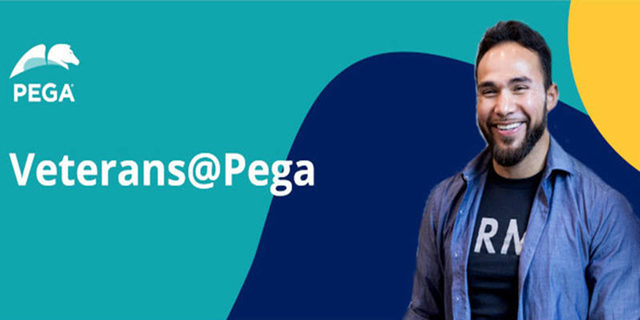
John Wolsborn